프로젝트 소개
이 프로젝트는 제가 18개월 동안 디자인하고 다듬은 3D 프린팅 온로드 RC 경주용 자동차를 소개합니다. 자동차 역학에 대한 열정을 가진 물리학 학생으로서, 저는 이 프로젝트를 통해 자동차 설계와 성능 원칙을 탐구하며 이론을 실습으로 연결하고자 했습니다. XF 모터스포츠, Indeterminate Design, Carroll Smith의 Tune to Win과 같은 자원으로부터 영감을 얻어 차량 동역학의 흥미로운 세계를 파헤칠 수 있었습니다.
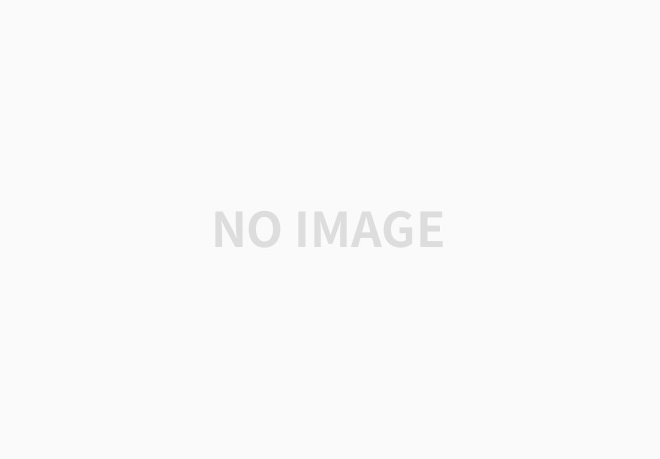
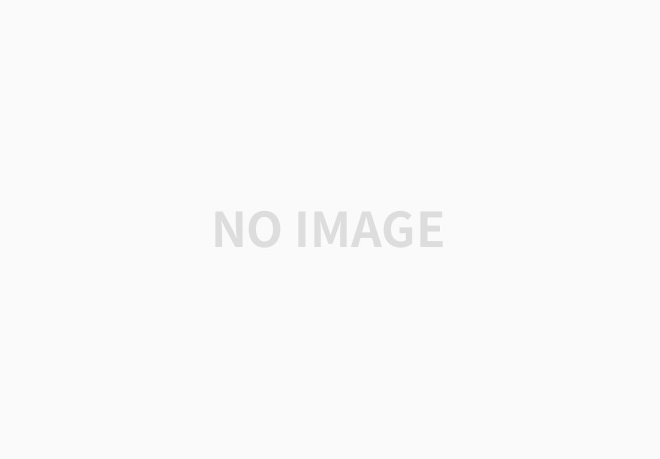
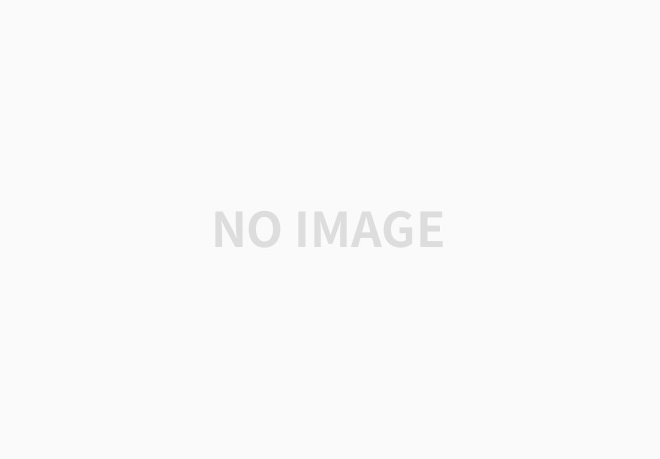
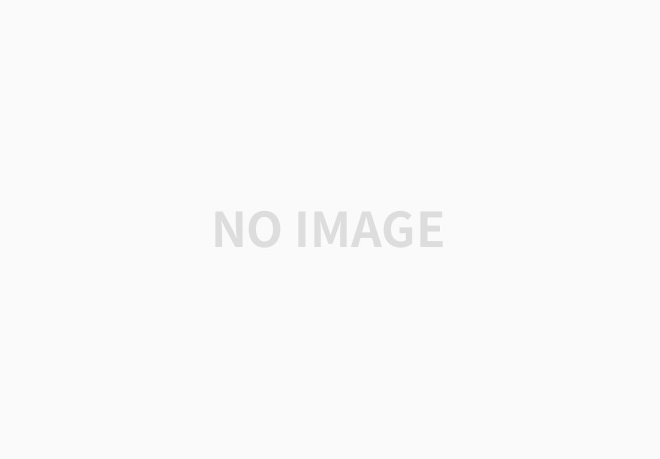
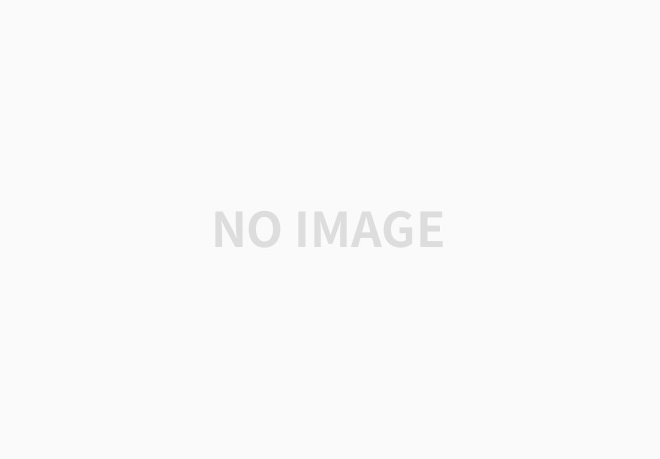
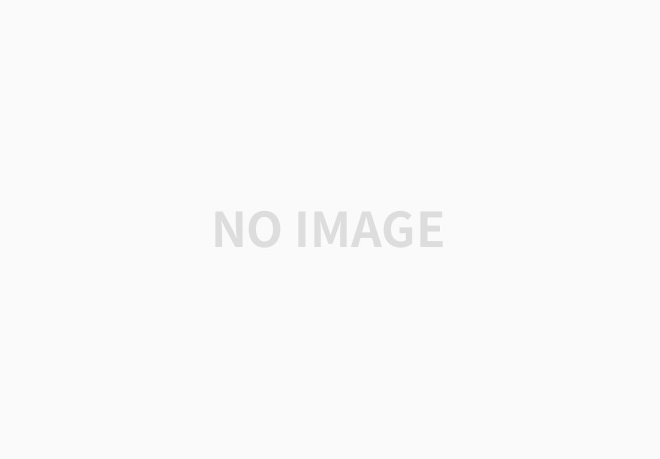
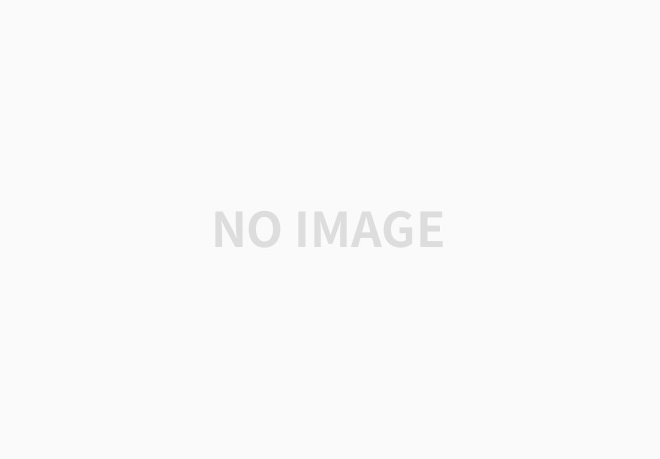
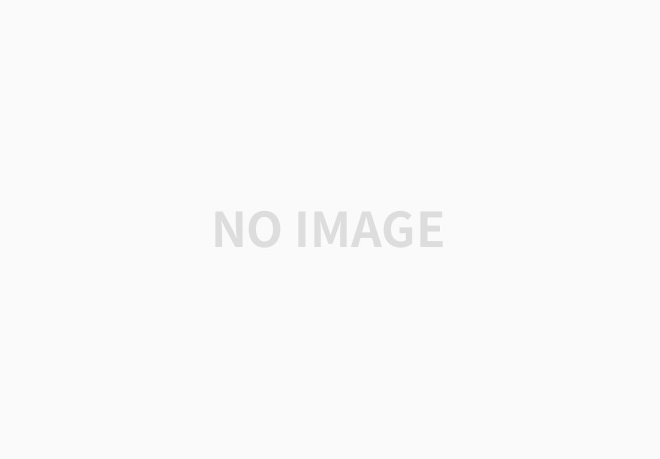
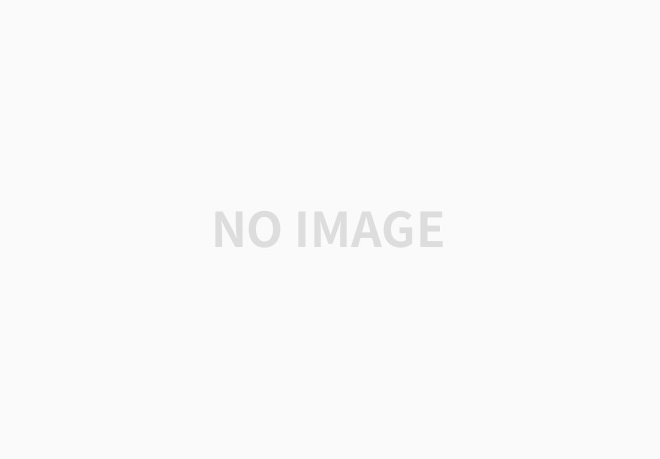
프로젝트 목표
RC 자동차를 설계하며 다음과 같은 목표를 설정했습니다:
- 온로드 포커스: 매끄러운 도로를 위한 설계, 오프로드 기능은 배제.
- 반응성과 예측 가능한 핸들링: 직관적이고 부드러운 운전을 목표로 오버스티어와 언더스티어를 제어 가능하게 설계.
- 후륜구동 및 디퍼렌셜 장착: 단순성과 운전의 재미를 위해 후륜구동 선택, 디퍼렌셜 추가로 코너링 성능 향상.
- 최적화된 중량 분배: 무거운 부품은 중심에 배치해 회전 관성을 줄임.
- 효율적인 서스펜션 설계: 접지력을 최대화하고 내부 마찰을 최소화하는 설계.
- 유지보수 용이성: 부품 교체와 서비스가 쉽도록 설계.
왜 이 프로젝트를 시작했을까?
저는 바퀴가 달린 모든 것에 매료되어 왔습니다. 어렸을 때부터 스턴트 스쿠터, 산악 자전거, 그리고 경주용 자동차까지 좋아했으며, 물리학을 공부하면서 자동차 설계의 이론을 실제 적용해보고 싶었습니다. Tune to Win을 읽고 YouTube에서 DIY 자동차 제작 프로젝트를 보며 이 프로젝트를 시작하게 되었습니다.
설계 원칙
서스펜션 기하학과 Ackermann 스티어링을 고려해 설계했으며, 범프 스티어를 최소화하여 예측 가능한 핸들링을 구현했습니다. Autodesk Fusion 360에서 2D 스케치를 사용하여 서스펜션 레이아웃을 초기 설계 단계에서 시뮬레이션하고, 데이터 분석을 통해 최적의 형상을 찾았습니다.
도전과 교훈
- 차량 동역학 배우기: 여러 설계 결정이 핸들링에 어떤 영향을 미치는지 배웠고, RC 자동차의 반응성과 성능을 체험하면서 실질적인 학습을 얻었습니다.
- 첫 번째 주요 3D 프린팅 프로젝트: 슬라이서 설정 및 공차 조정 방법을 배우며 반복적으로 프로토타입을 개선했습니다.
- Autodesk Fusion CAD 학습: CAD 설계의 기초를 배우고, 매개변수 사용을 통해 효율성을 높일 수 있었습니다.
반사
돌이켜보면 이 프로젝트는 RC 자동차를 만드는 것뿐만 아니라 3D 프린팅, CAD 설계 및 엔지니어링 원리에 대한 집중적인 학습 경험이기도 했습니다. 그 과정에서 많은 실수가 있었지만 그 모든 실수는 배우고 개선할 수 있는 기회였습니다.
RC-카1.0
공급
도구:
- 3D 프린터 (저는 Sovol SV07을 사용했습니다)
- 약 500g PLA
- 약 400g TPU/ 터프 PLA/ 모든 내충격성 필라멘트
- 납땜
- 납땜 인두 : 황동 인서트 설정을 위한 팁
- 나사(Torx 드라이브를 권장합니다) 및 너트용 도구
- 약간의 그리스
RC 관련 하드웨어:
- 4x HSP Wheel Axle 1/10 (부품 번호 02033)
- 4x HSP Hub 1/10, 베어링 포함(부품 번호 02014)
- 2x HSP Dogbone 77mm(부품 번호 08060) (77mm 길이로 광고된 Dogbone이 필요합니다. 핀 중심 사이의 거리는 실제로 72mm입니다.)
- 1x HSP 디퍼렌셜(부품 번호 02051) (샤프트가 긴 전면 버전이 필요합니다. 후면 버전을 사용하고 별도의 긴 샤프트를 구입하기만 하면 됩니다.)
- 4x 1/10 타이어(약 70 -75mm 외경) (이 모델의 12D 프린팅 림 대신 표준 HEX3 RC 자동차 림을 사용할 수도 있음)
- 4x 쇼크 업소버 50mm(스프링이 다른 비교적 좋은 것을 구입하는 것이 좋습니다(올바른 스프링 속도를 갖는 것이 매우 중요함)와 오일 댐핑이 있는 비교적 좋은 것을 구입하는 것이 좋습니다. "yes Racing Big Bore Go"를 사용합니다.
- 1x 송신기/수신기 콤보, ESC 및 540 모터. "Carlson Reflex X1", "Hobbywing 1060" 및 "Tamiya Torque Tuned"를 사용합니다.
- 모터 및 차동 장치용 1x 기어. 차동 장치의 내부 기어링은 1:3입니다. 모터 KV 등급과 호환되는 기어링을 사용하십시오. 저는 21개 이빨 48dp 모터 기어와 43개 이빨 48dp 차동 기어를 사용합니다. 그래서 제 총 기어링은 1:6.143입니다. 차동 기어의 직경은 2cm 미만이어야 합니다.
일반 하드웨어:
- M2 납작머리 나사:
- 8mm(8mm에서 12mm 사이의 모든 길이)(1개)
- M2 황동 인서트(길이 3mm)(1개)
- M3 납작머리 나사:
- 6mm(2개)
- 8mm(12배)
- 12mm(8배)
- 14mm(4배)
- 16mm(4배)
- 20mm(8배)
- 22mm(6배)
- 25mm(2배)
- 30mm(2개)
- 45mm(4배)
- 60mm(6배)
- M3 소켓 머리 나사:
- 18mm(2개)
- 20mm(2배)
- M3 초박형 헤드
- 8mm (4배)
- M3 황동 인서트(길이 5.7mm)(26x)
- M3 잠금 너트(18x)
- M3 사각 너트(2개)
- M3 와셔 (지름 6.7mm) (25x)
- M4 소켓 머리 나사
- 16mm (4배)
- M4 잠금 너트(8개)
- M4 와셔(직경 12mm 미만)(4x)
- 베어링 963 (x18)
- 베어링 MR105 (1x)
1단계: 일반 인쇄 설정 및 조립 팁
우리는 부품이 튼튼하기를 원하기 때문에 몇 가지 인쇄 설정이 매우 중요합니다.
레이어 사이의 우수한 접착력을 얻기 위해 저는 부품 냉각 팬을 사용하지 않고 대부분의 부품을 인쇄합니다. 브리징이 발생할 때만 100%로 설정합니다. 또한 낮은 일정한 유속으로 인쇄하는 것은 제 경험상 매우 좋은 결과를 보여주었습니다. 또한, 프린트를 과도하게 압출하는 경우, 소량은 레이어 라인 사이에 발생하는 작은 공극을 채워 레이어 접착력을 향상시키는 것으로 나타났습니다. 온도에 관해서는, 나는 제조업체 권장 사항의 더 높은 쪽에 인쇄했습니다. YouTube의 CNC Kitchen 비디오에서 "투명 FDM 인쇄는 분명히 더 강합니다!", 그 이유가 완벽하게 설명되어 있습니다. 느린 3mm로 인쇄합니다.3레이어 높이가 0.3mm인 0.6mm 노즐에서 /s를 사용하지만 이러한 방식으로 지속적으로 좋은 결과를 얻을 수 있습니다. 또한 연속 이음새에 약점이 생기는 것을 피하기 위해 무작위 이음새 위치를 사용하지만 더 중요한 것은 베어링이 구멍에서 실제로 동심원이고 정렬된 이음새로 인해 한쪽으로 밀려나지 않는다는 것입니다.
또한 일부 원통형 스페이서를 인쇄해야 합니다. 그들의 작은 크기 때문에, 그들의 직경은 인쇄 후에 의도한 것보다 보통 더 작습니다. 프린터의 경우 슬라이서에서 x-y-평면의 스페이서를 확대할 수 있습니다. M3 나사가 스페이서의 작은 나사산을 두드릴 때 조립 과정에서 도움이 되어 조립하는 동안 나사에서 떨어지지 않도록 하는 것이 도움이 된다는 것을 알았습니다.
달리 명시되지 않은 경우 모든 부품은 PLA로 인쇄됩니다.
참고로, 제가 프린트한 각 부품(하드웨어는 포함하지 않음)의 재질과 질량이 담긴 파일을 첨부했습니다.
작은 안전 예방 조치: 지지대를 제거할 때 보호 안경을 착용하십시오.
2단계: 개체 1 테스트
이런 식으로 시작하는 것은 약간 지루할 수 있지만 이 인쇄는 나중에 발생하는 모든 인쇄가 프린터에 따라 잘 보정되어 나올 수 있도록 합니다.
첫 번째 인쇄는 "TestObject1"입니다. 나머지 부분과 함께 사용할 설정으로 자르고 인쇄하십시오. 그림과 같이 모든 하드웨어가 구멍에 맞는지 확인하십시오. 베어링은 꼭 맞아야 합니다.
모든 것이 작동하면 "3단계: 테스트 개체 2"로 이동할 수 있습니다.
맞지 않는 것이 있으면 Autodesk Fusion에서 해당 매개변수(즐겨찾기로 표시된 매개변수)를 조정해야 하며, Autodesk Fusion에서 "TestObject1"을 내보내고 슬라이스하고 다시 인쇄해야 합니다. 이제 모든 것이 맞으면 "3단계: 테스트 개체 2"로 이동할 수 있으며, 그렇지 않은 경우 테스트 개체를 다시 조정하고 다시 인쇄해야 합니다.
Fusion 프로젝트에는 해결할 수 없는 매개변수 변경과 관련된 세 가지 오류가 있습니다. 그들은 모델에 문제를 일으킵니다.
3단계: 개체 2 테스트
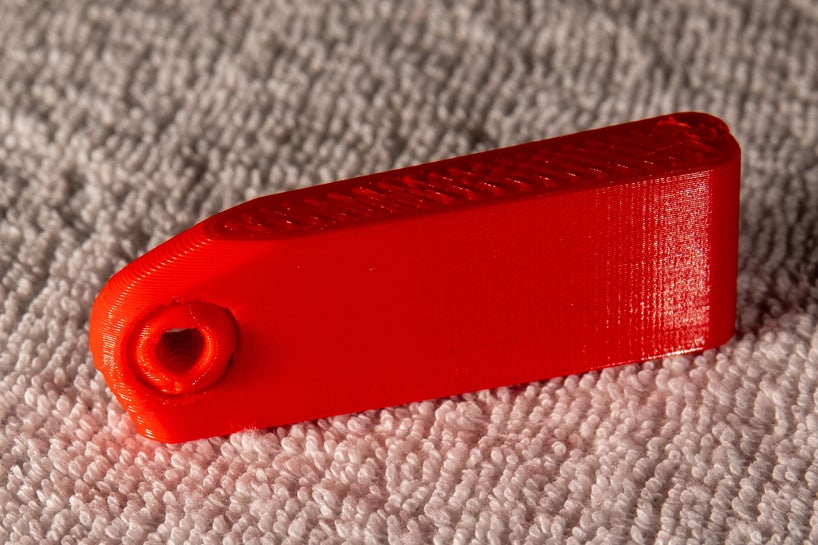
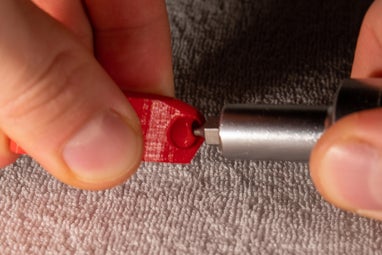
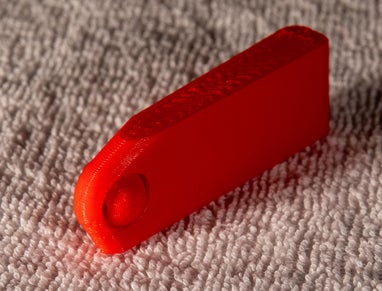
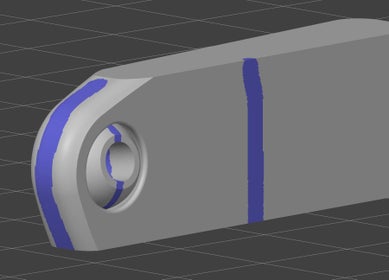
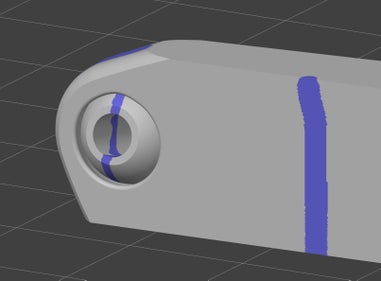
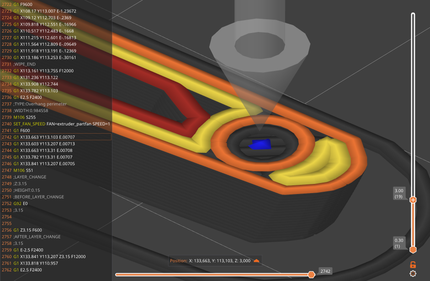
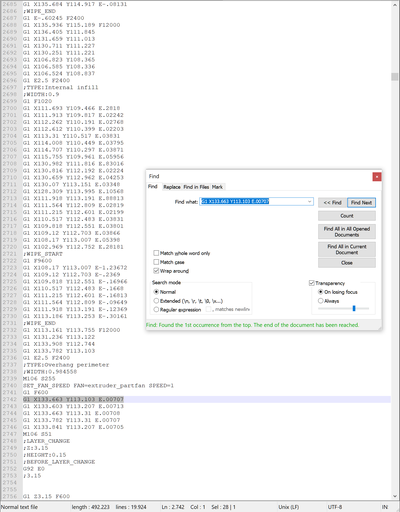
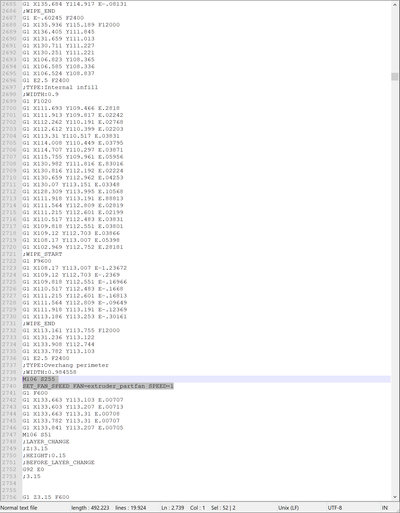
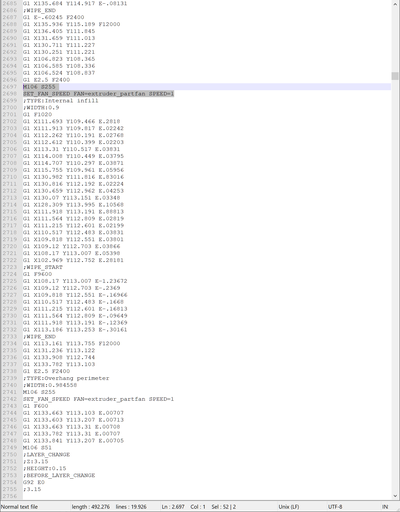
"TestObject2"는 프론트 위시본과 스티어 로드에 사용되는 구형 조인트를 프린팅하는 데 필요한 허용 오차를 결정합니다.
이 구형 접합을 현장 인쇄 개체로 인쇄하는 것이 이 프로젝트의 가장 고급 인쇄입니다. 구는 이음새의 배치 때문에 아래 또는 측면에 프레임에 많이 달라붙지 않고 "공기 중에" 인쇄되어야 합니다. 구가 프레임에 너무 많이 결합하면 분리될 수 없고 움직일 수 없습니다.
키가 작으면 많은 도움이 됩니다. 따라서 레이어 높이를 최대 0.15mm로 설정해야 합니다.
이 개체를 가장 좋은 방법으로 인쇄하려면 이음새를 올바른 위치에 배치하고 몇 개의 .gcode 줄을 수동으로 편집해야 합니다.
슬라이서에서 이음새에 페인트를 사용하여 그림 4와 5와 같이 이음새를 배치합니다. 파란색 선은 이음새가 설정되는 위치를 나타냅니다. 이음새는 구와 프레임에서 서로 옆에 있는 벽에 닿지 않아야 합니다.
.gcode를 내보낸 후 slicer-preview에서 구 인쇄를 시작하는 .gcode-command를 검색합니다(그림 6). 인쇄의 이 시점에서 부품 냉각 팬은 100%로 작동해야 합니다. 그러나 부품 냉각 팬을 0 %로 사용하여 다른 모든 것을 인쇄하기 때문에 먼저 100 % rpm으로 가속해야하며 1-2 초가 걸립니다. 따라서 100% 부분 냉각이 실제로 필요할 때 0에서 20% rpm 범위보다 팬을 얻습니다. 그러면 구가 프레임에 결합됩니다.
이 문제를 해결하기 위해 기본적으로 팬이 몇 줄 위로 100%로 이동하도록 명령을 이동했기 때문에 필요할 때 확실히 100% rpm에 있습니다.
구를 인쇄하기 시작하는 .gcode-line 을 적어 두십시오. 그런 다음 Notepad++와 같은 텍스트 편집기를 사용하여 .gcode 파일을 열고 정확한 .gcode 줄을 검색합니다(그림 7). 한 번 나타나야 합니다(정확히 구가 인쇄를 시작하는 위치입니다). 주어진 .gcode-line 위에는 "M106 255" 및/또는 "SET_FAN_SPEED FAN=extruder_partfan SPEED=1" 명령이 있어야 합니다. 이러한 명령은 부품 냉각 팬 속도를 100%로 설정합니다. 해당 명령을 복사하고 위에 몇 줄을 삽입하기만 하면 됩니다(그림 8). 이렇게 하면 팬이 더 일찍 가속되기 시작합니다. 파일을 저장하면 인쇄할 수 있습니다.
인쇄 후 M3 나사가 구멍에 맞는지 확인하십시오. 나는 정확한 동심원 맞춤을 보장하기 위해 이 구멍에 대해 약간 더 엄격한 공차를 선호합니다. 맞지 않으면 "Step2: Test Object 1"에 설명된 것과 동일한 방법으로 Autodesk Fusion에서 "PrintInPlaceBallJointHoleDia" 매개변수를 조정합니다. 그런 다음 HEX 드라이브를 사용하여 구를 케이지에서 부드럽게 분리해 보십시오. (보호 안경을 착용하십시오! 구가 케이지에 너무 많이 달라붙어 부품을 부러뜨리면 무언가가 눈 쪽으로 날아갈 수 있습니다.)
구가 케이지에 너무 많이 달라붙거나 너무 느슨한 느낌이 들면 "2단계: 테스트 오브젝트 1"에 설명된 것과 동일한 방식으로 Autodesk Fusion에서 "PrintInPlaceBallJointTolerance" 매개변수를 조정하고 모델을 내보냅니다. 불행히도 솔기 페인팅과 g.code 편집을 다시 해야 한다는 것을 잊지 마십시오. (fan 명령을 자동으로 이동하는 후처리 스크립트를 갖는 것은 앞으로 계획하고 있는 것입니다.) 다시 인쇄하고 허용 오차를 다시 확인하십시오.
매개변수가 마침내 프린터에 맞으면 다음 단계로 이동할 수 있습니다.
4단계: 프론트 로어 위시본
.gcode를 편집하기 위한 작업 흐름에 있는 동안 이 프로젝트에서 이러한 종류의 주의가 필요한 세 부분, 즉 프론트 위시본과 스티어 로드부터 시작합니다. 아래쪽 위시본을 인쇄하는 것으로 시작합니다.
우리는 다시...
- 레이어 높이가 구가 인쇄되는 위치에서 0.15mm보다 크지 않은지 확인합니다.
- 테스트 인쇄에서 했던 것처럼 이음새에 페인트를 칠하고,
- 테스트 인쇄에서 했던 것처럼 .gcode에서 fan 명령을 수동으로 이동합니다.
부품을 프린팅한 후에는 플라이어와 작은 육각 드라이브를 사용하여 지지 구조를 제거해야 합니다(그림 5-8). HEX 드라이브를 사용하여 구를 케이지에서 부드럽게 분리해 보십시오(그림 9 및 10). M3 사각 너트와 M3 소켓 헤드 20mm 나사(그림 11 및 12)를 사용하여 쇼크를 장착합니다.
하나의 전면 하단 위시본을 성공적으로 조립한 후 이 부분의 오른쪽 및 왼쪽 버전이 동일하므로 이 과정을 다시 반복합니다. 쇼크만 반대 방향으로 장착해야 합니다.
5단계: 프론트 어퍼 위시본
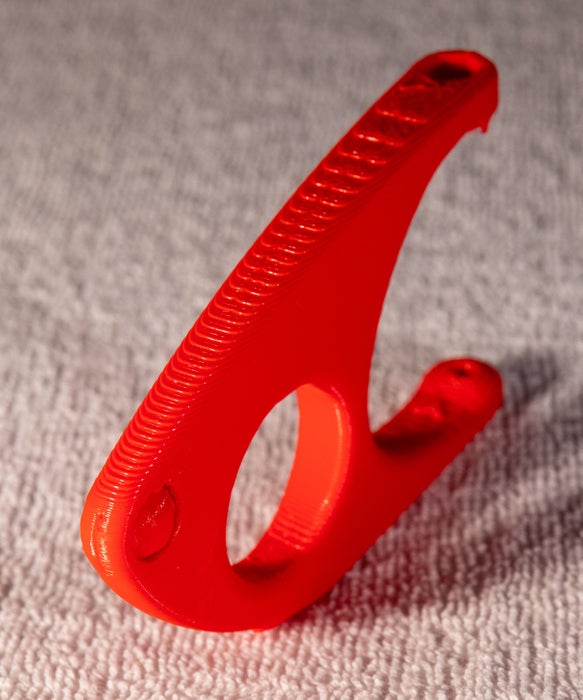
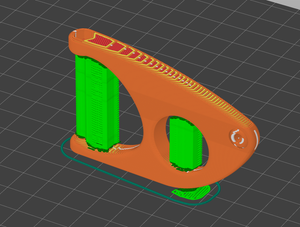
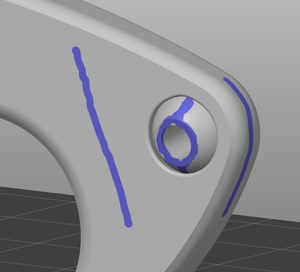
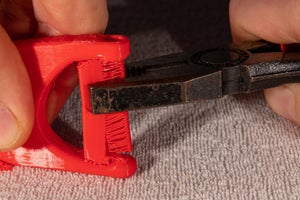
프로세스는 이전 단계의 프로세스와 동일합니다. 우리는 다시...
- 레이어 높이가 구가 인쇄되는 위치에서 0.15mm보다 크지 않은지 확인합니다.
- 테스트 인쇄에서 했던 것처럼 이음새에 페인트를 칠하고,
- 테스트 인쇄에서 했던 것처럼 .gcode에서 fan 명령을 수동으로 이동합니다.
부품을 인쇄한 후 플라이어를 사용하여 지지 구조를 제거해야 합니다. HEX 드라이브를 사용하여 구체를 케이지에서 부드럽게 분리해 보십시오.
슬라이서의 부품을 미러링하고 이 부분의 오른쪽과 왼쪽 버전이 동일하지 않고 대칭이므로 프로세스를 다시 반복합니다. 슬라이서에 파트를 미러링하면 솔기 페인팅을 다시 할 필요가 없기 때문에 시간을 절약할 수 있습니다(오른쪽과 왼쪽 파트를 따로 자르는 것과 비교).
6단계: 스티어 로드
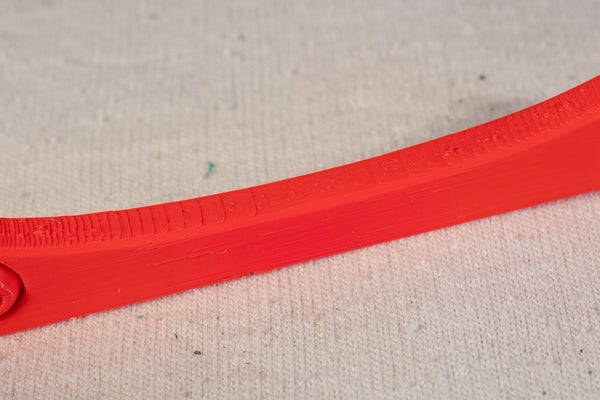
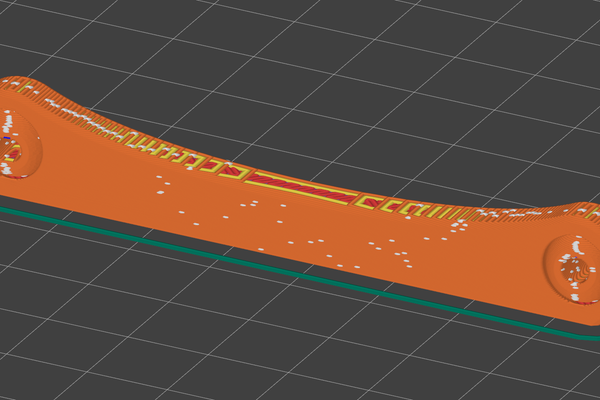
.gcode 편집이 필요한 마지막 부분입니다.
다시 말하지만, 프로세스는 부품당 두 개의(!) 구형 조인트가 있는 이전과 동일합니다. 우리는 해야 해요...
- 레이어 높이가 구가 인쇄되는 위치에서 0.15mm보다 크지 않은지 확인합니다.
- 테스트 인쇄에서 했던 것처럼 이음새에 페인트를 칠하고,
- 테스트 인쇄에서 했던 것처럼 .gcode에서 fan 명령을 수동으로 이동합니다.
부품을 인쇄한 후 HEX 드라이브를 사용하여 케이지에서 구를 부드럽게 분리해 보십시오.
이 부분을 두 번 인쇄하기만 하면 왼쪽과 오른쪽 버전이 동일하므로 사용할 수 있습니다.
7단계: 프론트 베이스
다음으로 인쇄할 부분은 FrontBase입니다.
인쇄할 때 몇 가지 지지대를 사용해야 합니다. 나무 지지대를 사용하는 것이 좋습니다. 펜치를 사용하여 제거하십시오.
비교적 긴 M3 나사, M3 너트 및 와셔(이 예에서는 한쪽에만 와셔를 사용하지만 양쪽에 하나씩 사용하는 것이 좋습니다)를 사용하여 원활한 작동을 위해 두 베어링 사이에 삽입해야 하는 베어링 스페이서를 잊지 않고 963 베어링을 제자리에 누릅니다.
다른 베어링에 대해 이 과정을 반복합니다.
8단계: 프론트 엔드 1 조립(위시본)
이 단계에서는 지금까지 인쇄한 모든 부품을 함께 조립하여 자동차의 프론트 엔드를 만들기 시작합니다.
M3 잠금 너트를 전면 하단 위시본에 삽입하는 것으로 시작합니다. M3 납작머리 나사(45mm)를 사용하여 전면 하단 위시본을 전면 베이스에 장착합니다. 쇼크의 장착 지점이 정렬되어 있는지 확인하여 오른쪽을 선택했는지 확인하십시오. 그런 다음 전면 상단 위시본에 M3 잠금 너트를 삽입하고 M3 납작머리 나사(45mm)를 사용하여 전면 베이스에 장착합니다. 그런 다음 M3 납작머리 나사(20mm), M3 와셔 2개 및 M3 잠금 너트를 사용하여 쇼크를 전면 베이스에 장착합니다.
움직일 때 상단 위시본이 충격과 충돌하지 않도록 하십시오. 이 경우 이쪽에 잘못된 상단 위시본을 장착하여 다른 것으로 교체해야 합니다.
반대쪽도 같은 방법으로 이 과정을 반복합니다.
구형 베어링에 약간의 그리스를 바르십시오.
9단계: 스티어링 레버 및 커플러
오른쪽 및 왼쪽 스티어링 레버를 인쇄하고 지지 재료를 제거한 다음 이전과 동일한 기술을 사용하여 베어링 스페이서가 있는 963 베어링을 구멍에 밀어 넣습니다.
스티어 레버 커플러를 인쇄한 후 963 베어링을 구멍에 밀어 넣습니다. 963 베어링은 이 부분에 매우 단단히 맞아야 합니다. 약간 더 높은 꽃 비율로 인쇄하면 구멍의 내경이 작아져 꼭 맞도록 합니다.
10단계: 프론트 엔드 2 조립(스티어링)
우리는 프론트 엔드를 조립을 계속합니다. M3 납작머리 나사(20mm)를 스티어 로드와 스티어 레버(그림과 같은 방향)에 삽입하고, 스티어 레버 위에 M3 와셔를 놓고, 그 위에 스티어 커플러를 놓고(베어링이 와셔를 향하도록) M3 잠금 너트를 거꾸로 장착하여 모든 것을 고정합니다.
다른 스티어 로드와 스티어 레버에 대해 이 과정을 반복합니다. 모든 것이 올바른 방향인지 확인하십시오.
M3 납작머리 나사(14mm)를 사용하여 포함된 베어링과 액슬이 있는 허브를 위시본에 장착합니다. 위시본과의 충돌을 피하기 위해 허브 장착 지점에 작은 모따기를 추가해야 할 수도 있습니다. 왼쪽 허브와 오른쪽 허브 사이에는 동일하지 않고 서로 대칭이기 때문에 약간의 차이가 있습니다. 스티어 로드용 허브의 장착 암이 지면에 더 가까운 방향인지 확인하십시오.
그런 다음 스티어 로드를 그림과 같은 구멍의 허브에 장착합니다. M3 납작머리 나사(20mm), M3 와셔 및 M3 잠금 너트를 사용하여 이 작업을 수행합니다.
M2 황동 인서트를 오른쪽 스티어 암에 삽입합니다. 다음은 나사산 황동 인서트를 삽입하기 위한 자습서입니다.
11단계: 전면 바닥판 및 상단 로드 연결부 인쇄 및 부착
전면 베이스와 전면 상단 로드 연결부를 인쇄하여 시작합니다. 부품에는 지지대가 필요하지 않습니다. 전면 상단 로드 연결 부분을 매우 강력하게 인쇄하십시오. 부품을 100% 입체로 인쇄했습니다. 이 단계에서는 프론트 탑 로드 연결부의 하단 부분만 프론트 엔드에 장착됩니다. 전면 상단 로드 연결의 상단 부분은 이후 단계에서 필요합니다.
두 개의 M3 황동 인서트를 전면 하단 플레이트에 삽입합니다.
6개의 M3 납작머리 나사(60mm)와 4개의 M3 와셔를 사용하여 전면 하단을 전면 하단 플레이트에 장착합니다. M3 와셔는 스티어링 레버 아래와 위에 있습니다. 전면 상단 로드 연결 하단 부분을 동일한 6개의 M3 납작머리 나사에 부착합니다.
12단계: 리어 로어 위시본
이 부분은 허브에서 리어 베이스로 많은 동력을 전달합니다. PLA를 사용하면 부품이 파손됩니다. TPU는 완벽하게 견딥니다. 테스트 중에 TPU 부품이 파손되지 않았습니다. 이번에는 첨가제로 인해 "일반" PLA보다 내충격성이 더 큰 Material4Print의 tough PLA를 사용해 보았습니다. 견고한 PLA는 이전에 사용했던 TPU보다 강성이 더 높습니다. 터프한 PLA는 첫 번째 테스트에서 잘 작동했지만 TPU 버전만큼 오래 테스트하지 않았습니다. 충격에 강한 재료를 사용하는 것 외에도 이 부분을 6개 이상의 벽으로 인쇄하는 것이 좋습니다.
인쇄 후 인쇄 후 하단 위시본의 지지 구조를 제거하십시오.
4개의 구멍 각각에서 963 베어링을 누릅니다.
M3 소켓 헤드 나사(18mm)와 M3 사각 너트를 사용하여 하단 위시본에 쇼크를 장착합니다.
두 개의 M3 납작머리 나사(12mm)와 인쇄된 스페이서를 사용하여 후면 허브를 하단 위시본에 부착합니다. - 이 Instructable의 사진을 찍는 동안 내가 뭔가 잘못했습니다. 왼쪽 허브를 오른쪽 하단 위시본에 장착했습니다. 두 개의 그림에서 노란색 원 영역의 "오류"를 찾을 수 있습니다. 허브 장착 암은 충격에 "더 가까울" 것입니다. 나는 나중에 이것을 알아 차리고 두 개의 허브를 교환했습니다. 이 단계의 마지막 그림은 완전히 조립되었을 때 허브의 올바른 방향을 보여줍니다.
슬라이서의 부품을 미러링하고 다른 쪽에 대해서도 이 과정을 반복합니다.
13단계: 리어 어퍼 위시본
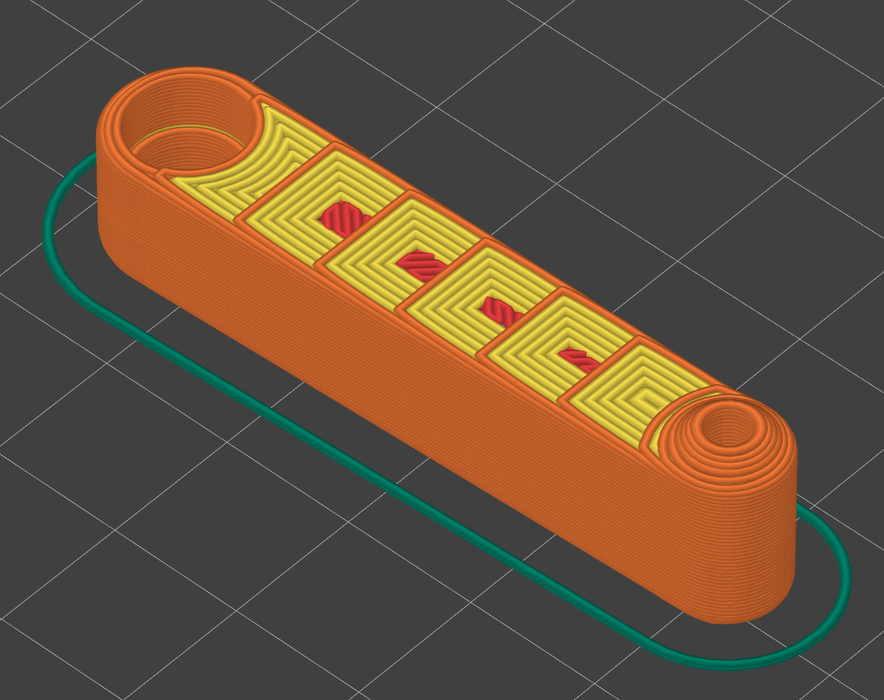
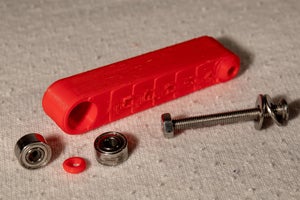
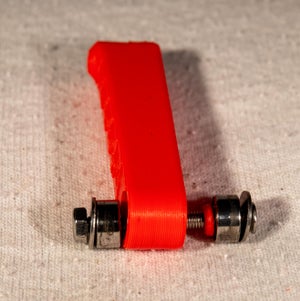
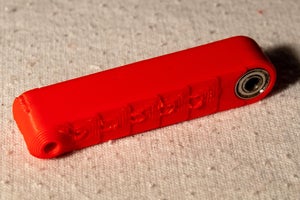
후면 상부 위시본을 인쇄한 후 이전과 동일한 기술을 사용하여 베어링 스페이서가 있는 두 개의 963 베어링을 구멍에 밀어 넣습니다. M3 잠금 너트를 제자리에 삽입합니다.
이 부분의 오른쪽 버전과 왼쪽 버전이 동일하므로 이 프로세스를 다시 반복합니다.
14단계: 리어 베이스
나무 지지대가 있는 후면 베이스를 인쇄하고 펜치로 제거합니다.
왼쪽과 오른쪽에 각각 스페이서가 있는 두 개의 963 베어링을 누릅니다.
납땜 인두를 사용하여 8개의 M3 황동 인서트를 구멍에 삽입합니다.
차동 장치를 후면 베이스에 느슨하게 놓습니다. 기름칠이 되어 있고 자유롭게 움직이는지 확인하십시오.
15단계: 리어 엔드의 조립
두 개의 M3 납작머리 나사(14mm)가 있는 두 개의 스페이서를 후면 하단 위시본에 부착합니다(그림 1 및 2).
도그본을 후면 하단 위시본을 통해 허브로 밀어 넣습니다(그림 3 및 4).
M3 납작머리 나사를 후면 베이스에 장착하고 도그본이 차동 장치와 허브에 있는지 확인합니다(그림 5 및 6).
M3 납작머리 나사, M3 와셔 2개 및 M3 잠금 너트를 사용하여 쇼크를 후면 베이스에 부착합니다(그림 7 및 8).
M3 납작머리 나사(30mm)를 사용하여 후면 상단 위시본을 후면 베이스에 장착합니다(그림 9 및 10).
M3 납작머리 나사(3mm)와 스페이서(그림 20 및 12)를 사용하여 후면 상단 위시본을 허브 상단 장착 지점(M3 나사산 포함)에 부착합니다. M3 와셔와 허브 장착 지점의 나사산에 카운터 너트 역할을 하는 M3 잠금 너트를 추가합니다(그림 13).
반대쪽에 대해서도 이 과정을 반복합니다(그림 14 및 15).
16단계: 후면 끝을 후면 바닥 플레이트에 부착
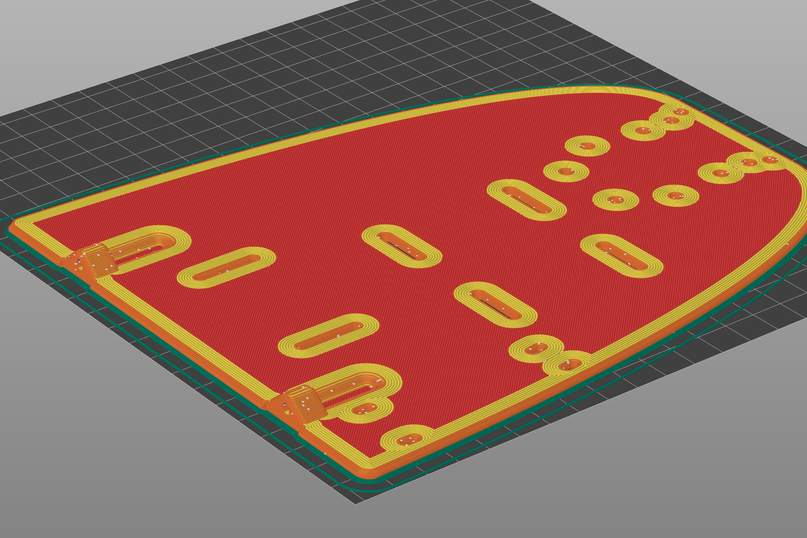
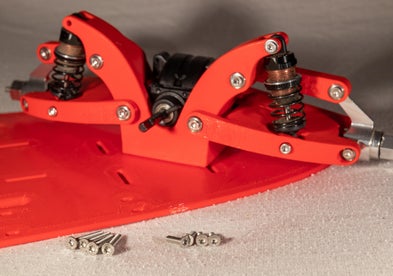
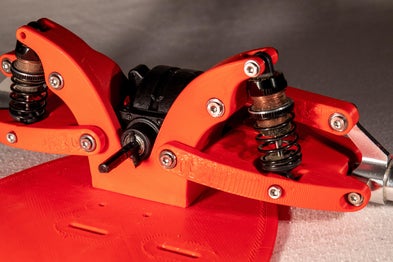
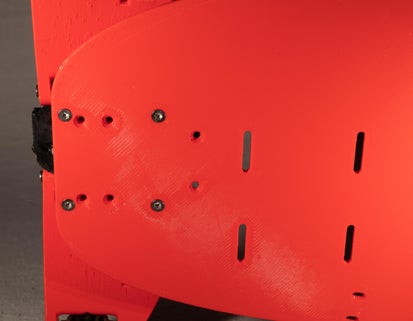
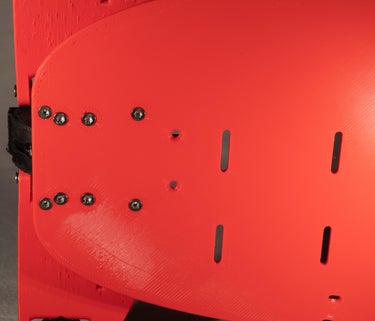
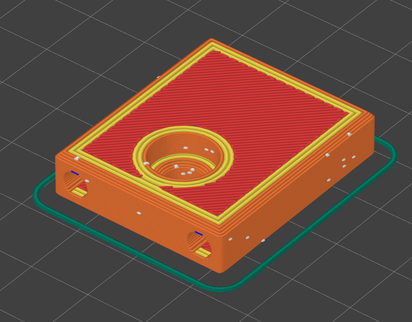
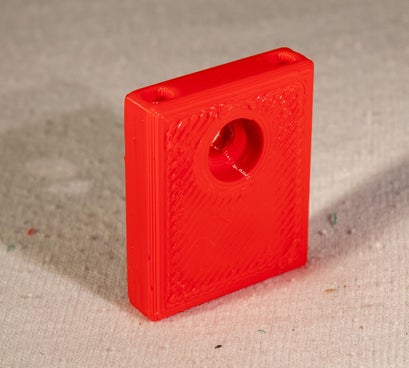

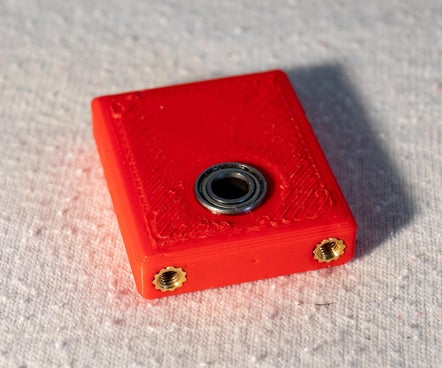
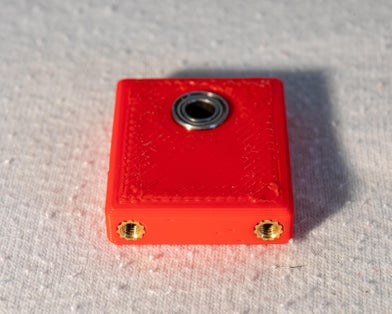
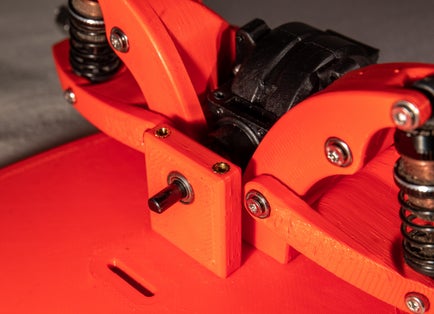
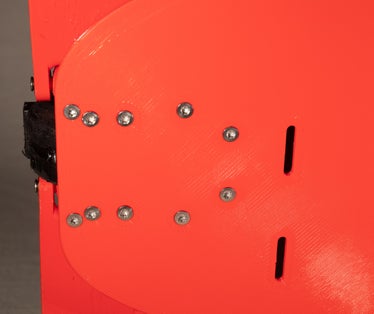
뒷면 바닥판을 인쇄합니다. M3 납작머리 나사(20mm 4개, 8mm 4개)를 사용하여 후면 하단을 후면 바닥판에 장착합니다. 그림 8와 같이 4mm 나사를 먼저 사용한 다음 그림 20와 같이 5mm 나사를 사용합니다.
차동 샤프트 지지 브래킷을 인쇄하고 MR 105 베어링을 누른 다음 납땜 인두로 4개의 M3 황동 인서트를 삽입합니다. 차동 샤프트에 밀어 넣고 그림 3과 같이 8개의 M12 납작머리 나사(12mm)를 사용하여 후면 바닥 플레이트에 장착합니다.
17단계: 후면 및 전면 바닥판 연결
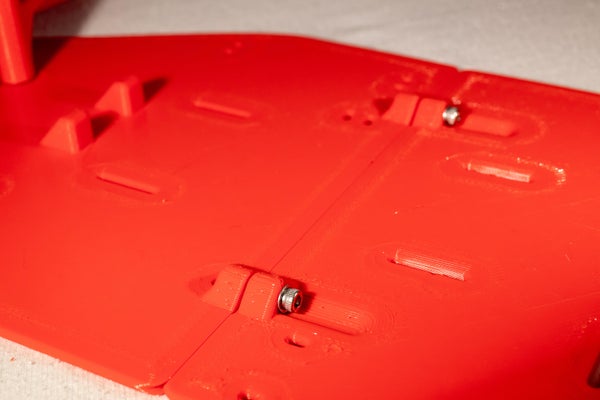
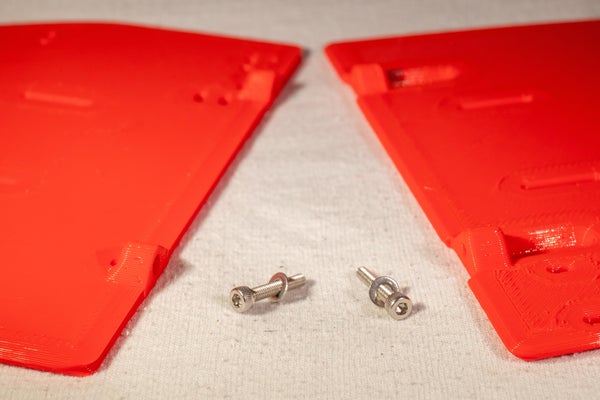
2개의 M3 소켓 헤드 나사(20mm)와 2개의 M3 와셔를 사용하여 후면 및 전면 하단 플레이트를 연결합니다.
18단계: 스티어링 서보 부착
두 개의 서보 장착 브래킷을 인쇄하고 두 개의 M3 황동 인서트를 각각 삽입합니다(그림 3).
서보 장착 브래킷을 서보에 장착합니다(그림 4 및 5).
4개의 M3 납작머리 나사(8mm)를 사용하여 서보와 서보 장착 브래킷을 전면 하단 플레이트에 부착합니다(그림 6).
양쪽 끝에 구형 조인트가 있는 M3 로드를 사용하여 서보 암을 오른쪽 스티어링 레버에 연결합니다(그림 7 및 8). 구형 조인트의 중심점 사이의 거리는 최적의 스티어링 동작을 위해 9.5cm입니다. 거리가 어긋나면 좌우 조향비가 약간 다릅니다.
19단계: 상단 막대 부착
읽기 상단 로드 연결부(그림 2)를 인쇄한 후 금속 사각 프로파일을 부착합니다.file (8x8mm, 40.4cm)를 후면 상단 로드 연결, 4개의 M3 납작머리 볼트(mm) 및 4개의 M3 와셔(그림 1 및 3)를 사용하여 후면 끝에 연결합니다.
금속 사각형 프로파일을 부착합니다.file 전면 상단 연결부, 6개의 M3 잠금 너트 및 6개의 M3 와셔를 사용하여 전면 끝에 연결합니다.
좋은 정렬을 보장하기 위해...
- 바닥판이 매우 평평한 표면에 서 있는 동안 이 장착 과정을 수행하십시오. 이렇게 하면 전면 또는 후면 끝이 한 평면에 있지 않을 때 알 수 있습니다.
- 모든 볼트와 너트를 한 번에 조금씩만 조이십시오. 이렇게 하면 조금씩 정렬 불량을 수정할 수 있습니다.
상단 막대를 부착하는 작업이 끝나면 이전에는 매우 유연했던 전체 구조가 어떻게 극도의 강성을 얻었는지 알 수 있습니다. 그 정확한 이유는이 Instructable의 끝에 설명되어 있습니다.
20단계: 모터 부착
차동 장치의 샤프트에 차동 기어를 장착하여 시작합니다(그림 1 및 2). 48 dp 43 t 기어를 사용했습니다. 여기에 나사 잠금 접착제를 사용하십시오.
모터 장착 브래킷 (그림 3)을 PETG와 같은 내열성 재료 또는 제 경우에는 견고한 PLA로 인쇄하고 4 개의 M3 황동 인서트 (그림 4)를 삽입합니다. 두 개의 M3 납작머리 나사(6mm)를 사용하여 모터를 모터 장착 브래킷에 부착합니다(그림 5 및 6).
4개의 M3 초박형 머리 나사(8mm)를 사용하여 장착 브래킷이 있는 모터를 후면 바닥판에 장착합니다(그림 7, 8, 10).
모터 기어를 모터에 부착하여 차동 기어와 잘 맞물리도록 하고 그 사이의 거리를 적절하게 설정합니다(그림 9 및 10). 다음은 거리를 올바르게 설정하는 방법에 대한 자습서입니다. 기어에 그리스를 바르십시오.
21단계: 전자 장치
이 단계에서는 모든 전기 부품을 배선하고 해당 슬롯에 지퍼 타이와 두꺼운 양면 접착 스트립을 사용하여 제자리에 고정합니다. 전기 부품을 배선할 때는 항상 제조업체 설명서를 참조하십시오. 다음은 기본 RC 전자 장치에 대한 자습서와 RC 커넥터 납땜에 대한 자습서입니다.
구성 요소를 납땜해야 하는 경우 항상 환기가 잘 되는 곳에서 작업하고 연기에 대한 노출을 최소화하십시오.
22단계: 바퀴 부착
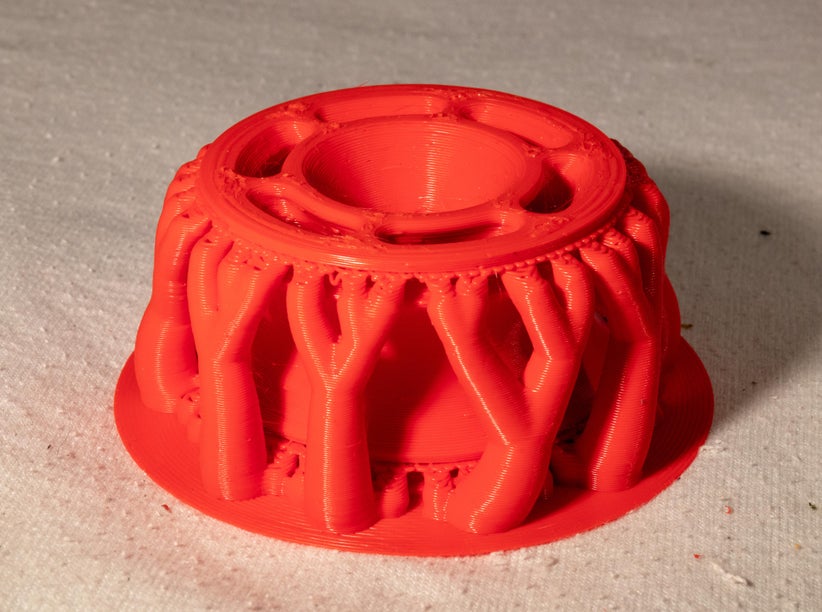
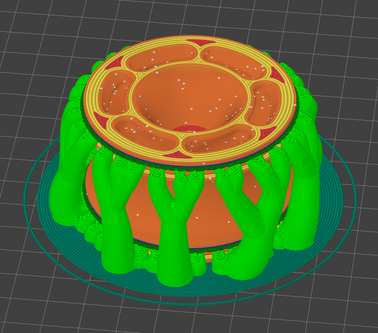
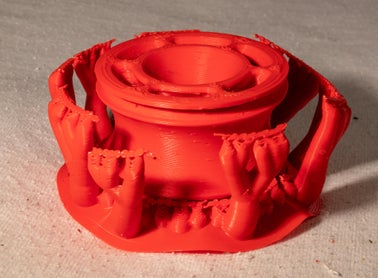
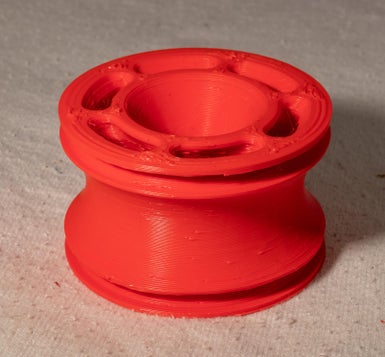
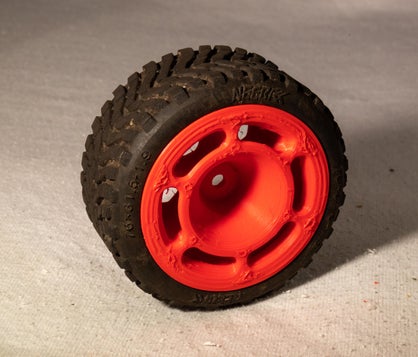
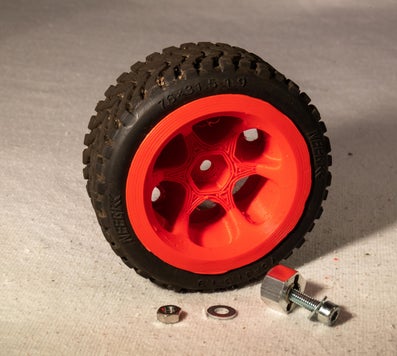
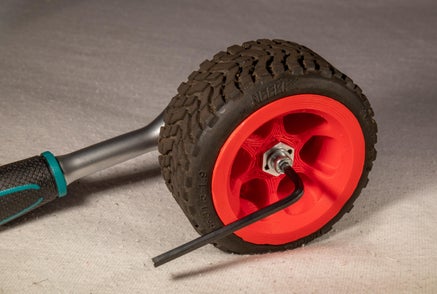
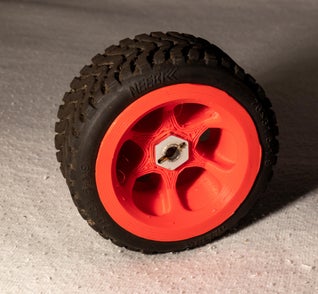
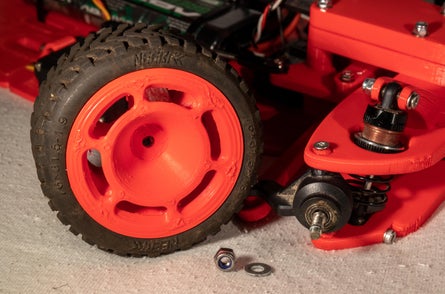
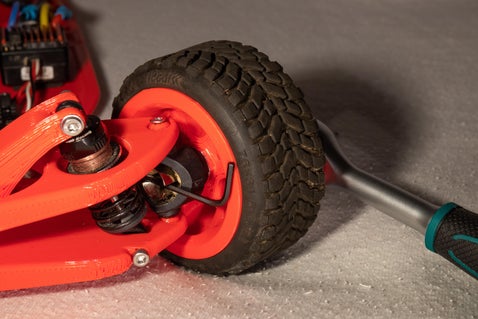
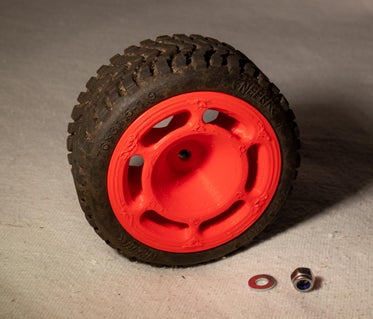
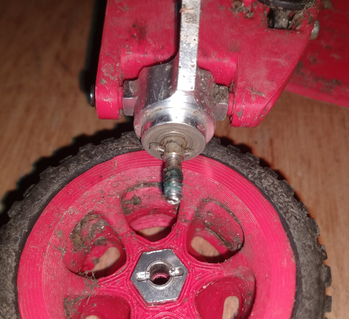
나무 지지대를 사용하여 테두리를 인쇄하고 펜치로 제거합니다(그림 1-4). 타이어를 림에 끼웁니다(그림 5). 허브 어셈블리의 일부인 HEX12 너트를 M4 나사, 와셔 및 너트로 해당 구멍에 눌러 단단히 끼웁니다(그림 6 및 7).
이 과정을 네 번 반복합니다.
8mm 소켓 렌치와 9mm 육각 렌치를 사용하여 동력 전달을 위한 허브 축의 핀 없이 각각 M4 잠금 너트와 M4 와셔가 있는 두 개의 조립된 휠(그림 2.5)을 프런트 엔드의 허브(그림 10)에 부착합니다. 우리는 전면에서 동력 전달이 필요하지 않으며 이러한 방식으로 베어링 예압을 미세 조정할 수 있습니다.
조립된 다른 두 개의 휠을 같은 방식으로 리어 엔드의 허브에 부착하되 동력 전달을 위해 허브의 액슬에 핀을 설치합니다(그림 11 및 12). 몇 달간의 테스트 끝에 핀이 부러져서 완벽하게 맞는 M2 나사산 막대로 교체했습니다.
23단계: 프론트 범퍼 부착
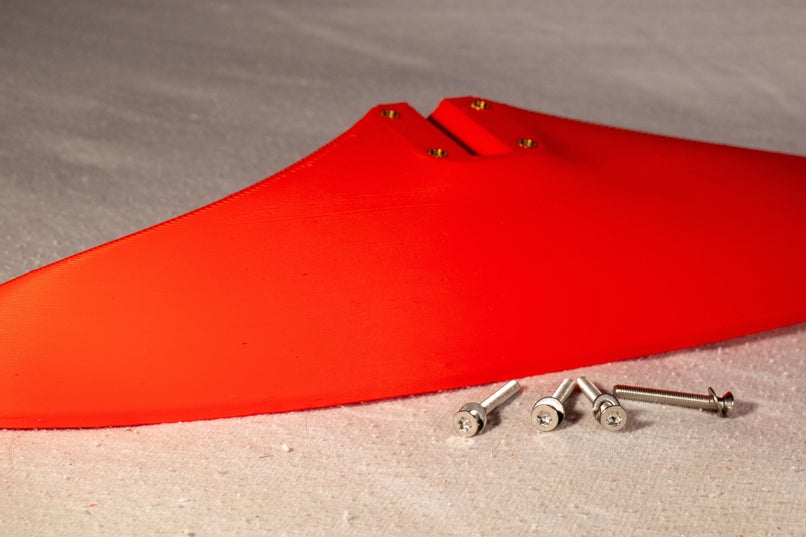

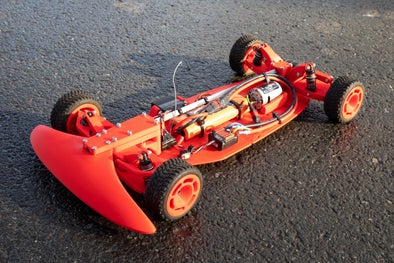
마지막으로 부착할 부품은 프론트 범퍼입니다.
충격에 강한 소재를 사용하는 것이 좋지만 PLA는 높은 벽 두께로 인쇄하면 충돌 시 자동차를 구하는 데 정말 좋은 결과를 보여주었습니다.
4개의 M3 황동 인서트를 삽입하고 프론트 범퍼를 탑 로드에 부착합니다.
갈 준비가 되었습니다!!
24단계: 지오메트리 및 서스펜션 설계
이 RC카를 디자인할 때 저는 약 1:10의 스케일을 목표로 하기로 결정했습니다. 이 크기는 구성 요소를 위한 충분한 공간과 관리 가능한 전체 빌드 사이의 균형을 제공했습니다. 리어 디퍼렌셜, 도그본 스타일의 구동축, 휠 허브를 구입하는 것부터 시작해 리어 트랙 너비(22.3cm)를 설정했습니다. 프론트 트랙 너비의 경우 코너링 시 안정성과 견인력을 향상시키기 위해 약간 더 넓은 치수(23.5cm)를 선택했습니다.
휠 베이스에 대한 트랙 너비의 비율은 또 다른 주요 고려 사항이었습니다. 실제 디자인 및 다른 RC카와 비교한 결과 1:1.6 비율을 선택했는데 휠베이스가 36.6cm가 되었습니다. 이 구성은 특히 고속 코너링 시 안정적이고 예측 가능한 핸들링을 촉진하기 위해 선택되었습니다.
서스펜션 트래블은 약 15-20mm로 설정되었으며, 여기에는 압축과 리바운드가 모두 포함됩니다. 이를 통해 휠은 직경의 약 20-25%를 압축할 수 있습니다. 소형 차량의 경우 아스팔트의 상대적으로 거친 질감을 감안할 때 이 서스펜션 이동이 필요합니다.
그립을 극대화하기 위해 저는 서스펜션이 압축될 때 캠버가 거의 선형으로 증가하도록 서스펜션 지오메트리를 설계했습니다. 이것은 코너링 또는 범프와 같은 동적 조건 동안 일관된 접촉 패치를 보장합니다. 롤 센터는 낮게 배치되었으며 여러 시나리오에서 안정적으로 유지되어 차량의 예측 가능한 핸들링에 기여했습니다. 또한 10°의 캐스터 각도를 구현하여 가장 필요할 때 코너링 중에 동적 캠버를 추가합니다.
서스펜션 트래블이 의도치 않게 스티어링 각도를 변경하는 문제인 범프 스티어는 신중한 조정을 통해 최소화되었습니다. 스티어링 시스템은 Ackermann 형상을 근사화하지만 측면 중량 전달을 고려한 수정 사항이 포함되어 있습니다. 코너링 중 접지력이 향상된 바깥쪽 휠은 안쪽 휠보다 더 급격하게 회전하도록 설정되어 코너링 성능을 최적화합니다.
다이빙 방지 지오메트리는 제동 구성 요소가 없어 불필요하고 큰 이점 없이 복잡성이 추가되었기 때문에 포함되지 않았습니다.
이미 지적했듯이 저는 서스펜션 지오메트리 전문가와는 거리가 멀기 때문에 이 점을 염두에 두십시오. 서스펜션 형상에 대해 자세히 알고 싶은 분들은 XF Motorsports의 이 소개 비디오를 강력히 추천합니다.
25단계: 강도 및 강성
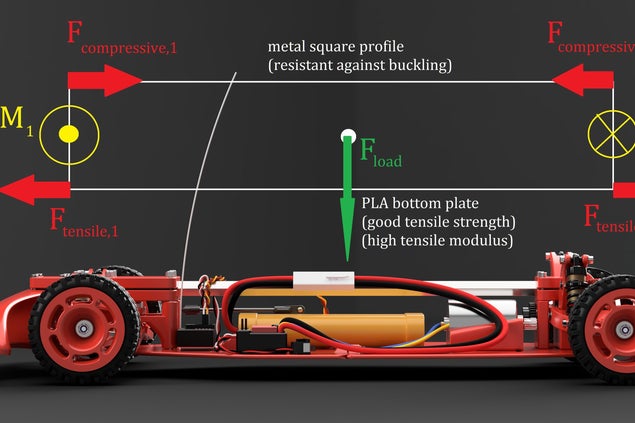
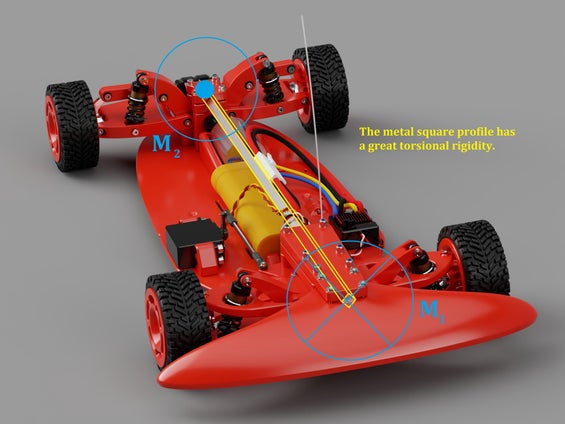
그림 1 : 자동차가 바퀴로 움직일 때 자체 중력과 주행 역학에 의해 유발된 추가 하중을 보상합니다. 이 모든 힘을 가정할 때 F부하, 무게 중심에서의 공격, 두 개의 반대 토크, M1 및 M2 자동차의 앞쪽과 뒤쪽 끝에 만들어집니다. 반대 토크를 통해 상단 로드는 압축력을 받고 하단 플레이트는 인장력을 받습니다. 금속 상단 로드는 좌굴에 매우 강하며 PLA로 만든 바닥 플레이트는 인장 계수와 강도가 높습니다. 결과적으로 시스템은 매우 경직되어 있습니다.
그림 2 : 자동차가 왼쪽 또는 오른쪽의 범프를 넘어 주행하는 경우 앞뒤 끝에서 반대 토크가 유도됩니다. 사각 프로파일 상단 로드는 이러한 비틀림 힘에 대한 저항에 가장 크게 기여합니다. 정사각형 프로파일은 원통형 프로파일보다 비틀림 힘에 대한 저항이 적지만 자동차의 전면과 후면에서 상단 로드 연결로 클램핑하는 것이 훨씬 쉽습니다. 원통형 상단 막대를 사용하면 둥근 막대가 상단 막대 연결에서 약간 회전할 수 있었기 때문에 훨씬 더 많은 비틀림 처짐이 발생했습니다. 정사각형 프로파일을 가진 자동차는 상단 로드만큼만 비틀림 편향을 경험할 수 있으며, 이는 8x8mm 티타늄 정사각형 프로파일(또는 알루미늄 또는 강철)로 거의 무시할 수 있습니다.
또한 정면 충돌의 경우 충격이 프론트 범퍼에서 탑 로드를 통해 차량 전체로 분산되어 단일 부품에서 충돌 스파이크가 줄어듭니다.
이 블로그는 제 작업과 경험을 공유하기 위한 기록이며, 누구나 자신만의 RC 자동차 설계에 도전할 수 있도록 영감을 드리기를 바랍니다! 🚗💨
'모빌리티 프로젝트' 카테고리의 다른 글
Bob The Robot: 아두이노 기반 로봇 프레임워크 제작기 (0) | 2025.03.28 |
---|---|
4족 이동 로봇 설계 및 제작 (0) | 2025.03.25 |
[속보] 국민연금 개혁: 첫째 출산 및 군복무 크레디트 최대 12개월 인정 확대 (0) | 2025.03.20 |
혁신적인 Two Bar Vertical Lift: 디자인부터 제작까지 (0) | 2025.03.19 |
TinkerCAD로 2D 이미지를 3D 신발 매력으로 변환하는 방법 (0) | 2025.03.19 |